The Lean methodology differs from traditional project management by focusing on delivering value from the customer’s perspective. According to the Lean model, continuous improvement is paramount, and each member of the project team is responsible for improving individual processes. To show how this works, let’s first take a closer look at the basics of Lean and their role in project management.
What is Lean Project Management?
Lean Project Management is a business philosophy, not just a set of tools or an improvement method. The methodology emphasizes the elimination of waste in all business processes in order to reduce project cost and time while increasing quality.
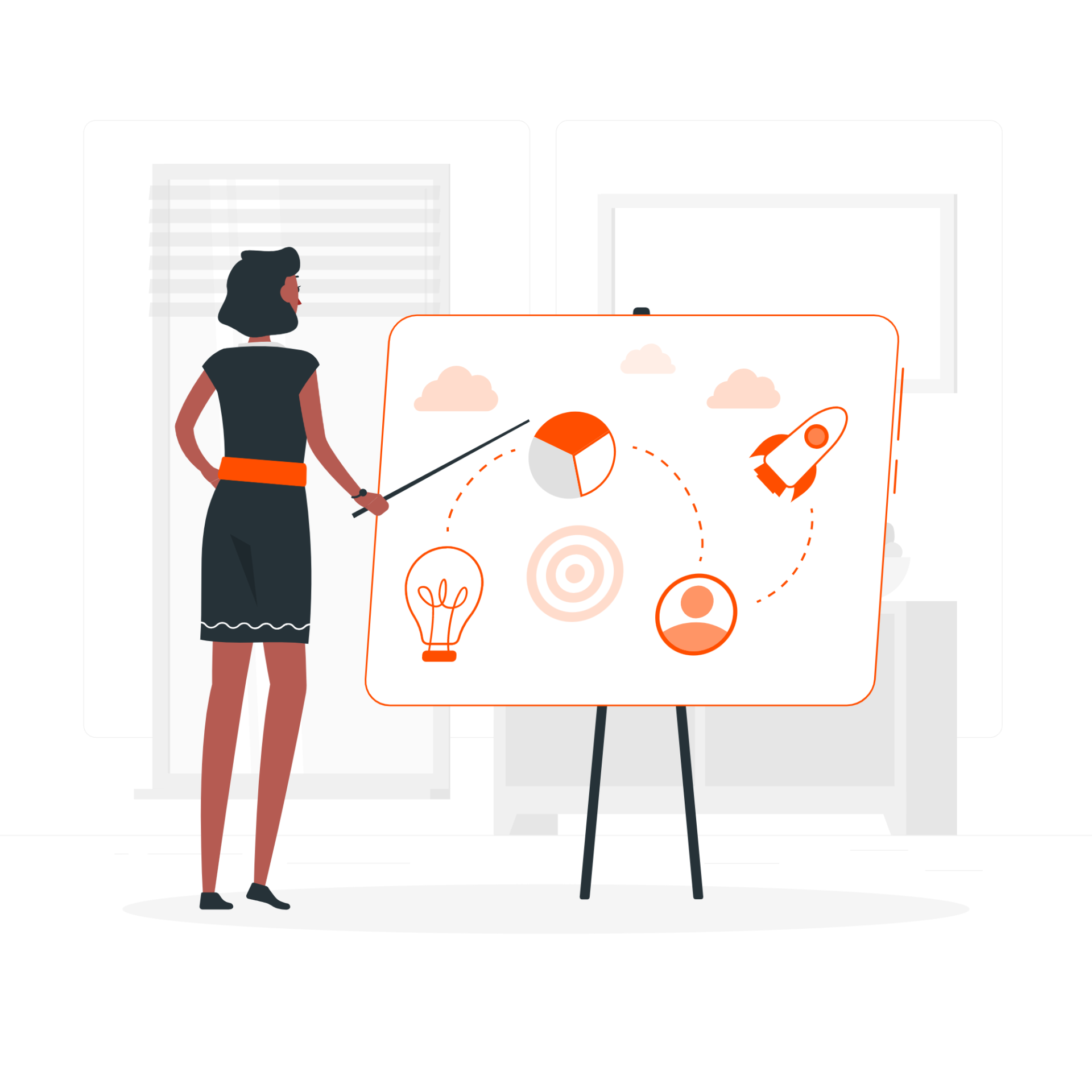
Main assumptions of Lean methodology
According to Paul Akers, an internationally recognized expert in Lean Management, the core of Lean implementation are three concepts without which project management becomes tedious and unproductive.
RECOGNIZING WASTE
The key to success is to identify waste so that you can further eliminate it. Within the Lean methodology, three types of wastes have been identified. These include:
- Muri – waste caused by irregularities in work,
- Mura – waste due to overloading of machinery and people,
- Muda – waste that arises from performing an activity that does not add any value.
DAILY IMPROVEMENTS
Once waste has been identified, efforts can be directed to gradually eliminate it. No problems can be completely ruled out right away, so consistent daily efforts are important.
RECORDING IMPROVEMENTS
Although it may sound strange, recording the effects of improvements in “before” and “after” form, preferably in the form of videos, greatly accelerates and develops a Lean culture within the team. The recordings can be available to all members of the company’s management team and serve as a way to standardize improvements.
Lean Project Management Process
The Lean methodology is based on five principles focused on process improvement.
DETERMINE CUSTOMER VALUE
Every company strives to provide a service or product that the customer is willing to pay for. To achieve this, it is necessary to look at the service or product from the customer’s point of view, because value is “everything the customer is willing to pay for”. Furthermore, value is anything that generates customer satisfaction. Sometimes teams need to introduce qualitative and quantitative techniques in the form of surveys, interviews or polls to determine customer value. This is especially true for new products and services where customers are unsure of their requirements.
IDENTIFY THE VALUE STREAM
In this step, you should analyze all the activities that take place during the time between placing the order and releasing the finished product or completing the service. This allows you to verify how each step in the process contributes to the outcome, so you can identify and eliminate waste.
ENSURE A CONTINUOUS WORKFLOW
Once waste has been removed, it is necessary to establish a seamless flow of value-generating processes. This includes breaking the process into independent steps, removing delays, redistributing workloads, and reconfiguring process steps.
DEVELOP A SYSTEM FOR DELIVERY OF PRODUCTS AND SERVICES
In this step, develop a system for delivering products and services to the customer at the time and in the quantity required by the customer. You should minimize any inventory and run the system only when the customer places an order. This optimizes the efficiency of resources and eliminates all operations that consume time, space and money.
LOOK FOR CONTINUOUS IMPROVEMENT
To effectively eliminate waste and maximize productivity and efficiency, the entire project process should be evaluated regularly and improvements made accordingly.
Lean Project Management – in which projects will it work?
Although Lean is used in companies of many types and sizes, it works best (at least initially) for small projects and small teams because it requires strong communication. Of course, as the company grows, the Lean methodology can be sustained among new team members.
Benefits of applying Lean methodology in IT projects
The implementation of Lean methodology into the management of projects carried out by software house teams should, in the long run, result in a change of the organization’s culture. The benefits of implementing Lean concepts include:
- process simplification – continuous workflow improvement means getting rid of wasteful activities, resulting in simplified processes and easier management;
- cost reduction – this is the result of eliminating waste and streamlining processes;
- motivated employees – employees who spend time doing valuable work naturally take more initiative and are more committed to the project at hand;
- greater value for customers – focusing on delivering added value naturally allows you to better execute IT projects and deliver higher quality products and services.
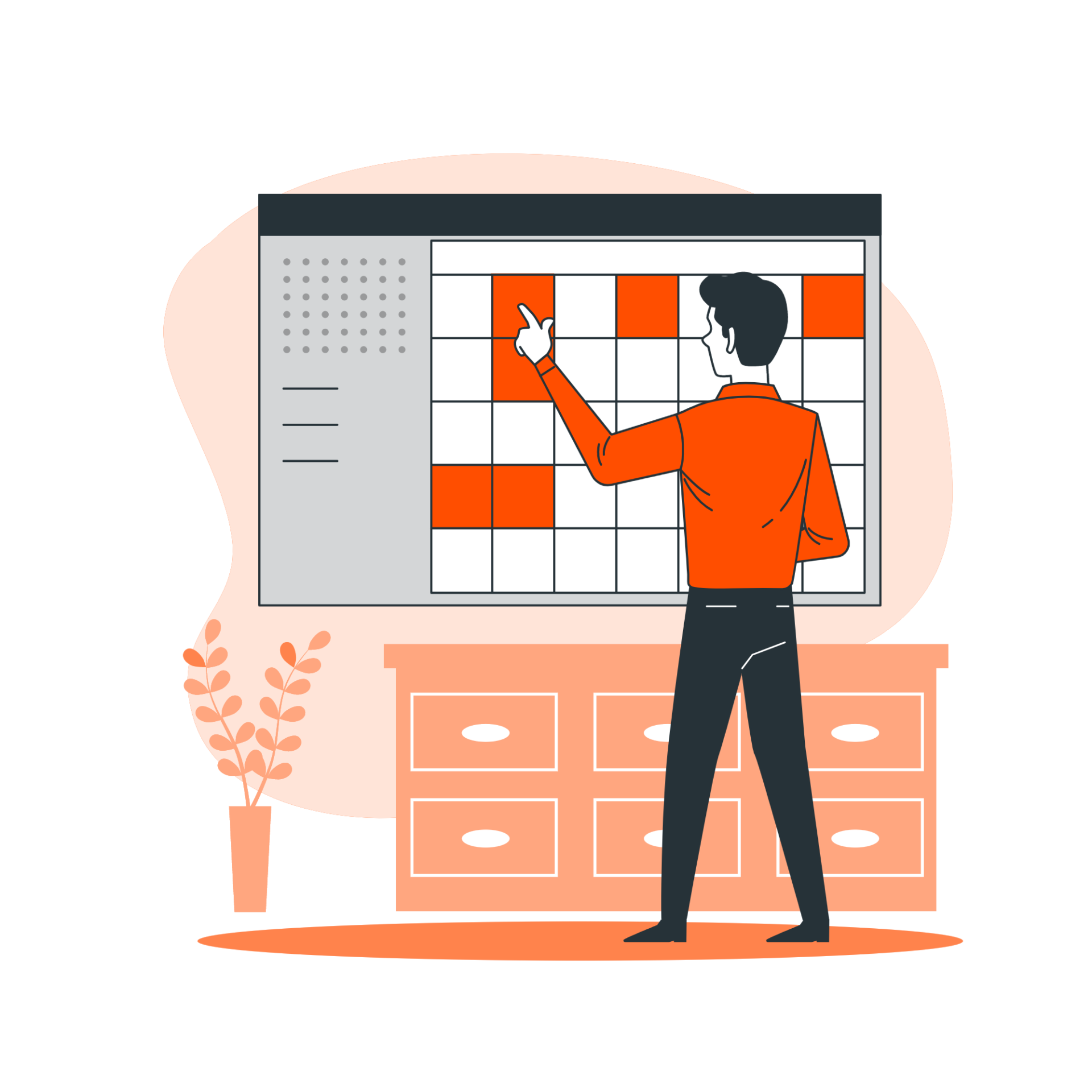
Methodology implementation – Lean and Agile go hand in hand
Both the Lean methodology and the Agile concept have found their place in the software house industry. Agile focuses on iterative development while maintaining process flexibility. Lean emphasizes the elimination of wasteful activities that do not generate added value. While these are distinct methodologies, they share the same core values. IT teams can use a hybrid of Lean and Agile approaches to build healthy, innovative teams that consistently deliver value to the customer.
When executing IT projects at Da Vinci Studio, we are driven by the needs of our clients and their businesses. A natural consequence of our approach is the implementation of the Lean methodology into the undertaken activities. This allows us to create personalized web applications and mobile applications that meet the expectations of our clients. Contact us and find out what we can do for you.